Technology Readiness Levels (TRLs) are a method for understanding the technical maturity of a technology during its acquisition phase. TRLs allow engineers to have a consistent datum of reference for understanding technology evolution, regardless of their technical background. TRLs are designated through a Technology Readiness Assessment (TRA), which examines a programme's concepts, technology requirements, and technology capabilities.
If you have any questions or need help, email us to get expert advice:
contactus@twi.co.uk
Originally developed by NASA in the 1970s for space exploration technologies, TRLs assess the maturity level of a technology throughout its research, development and deployment phase progression. TRLs are based on a scale from 1 to 9, with 9 being the most mature technology.
Many organisations have implemented TRLs for their own purposes, with certain organisations, such as the European Union (EU), further normalising the NASA readiness-level definitions, allowing for easier translation to multiple industry sectors – not just space exploration.
The EU defines the nine levels as follows:
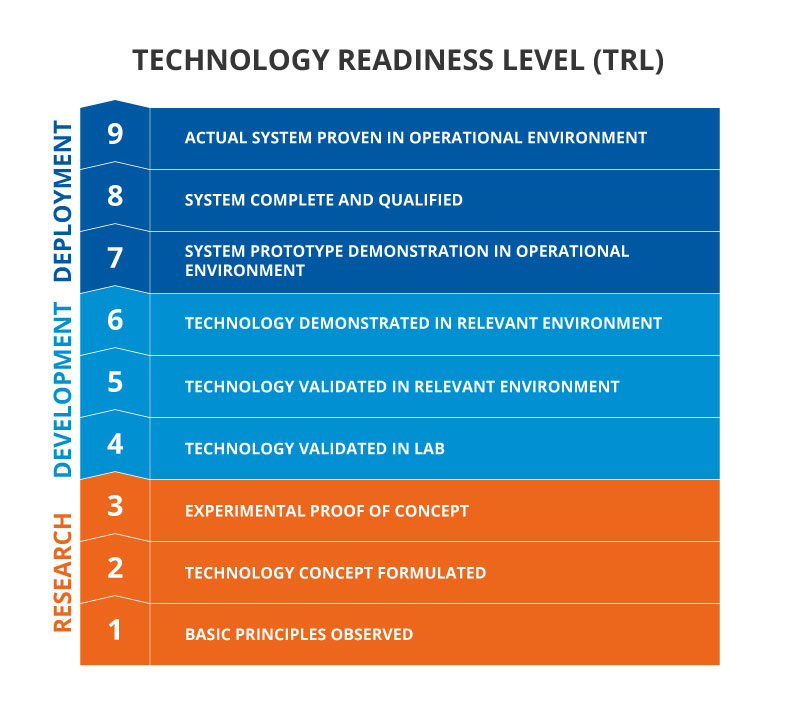
TRL scale diagram
TRL | Description | Example |
1 |
Basic principles observed |
Scientific observations made and reported. Examples could include paper-based studies of a technology’s basic properties. |
2 |
Technology concept formulated |
Envisioned applications are speculative at this stage. Examples are often limited to analytical studies. |
3 |
Experimental proof of concept |
Effective research and development initiated. Examples include studies and laboratory measurements to validate analytical predictions. |
4 |
Technology validated in lab |
Technology validated through designed investigation. Examples might include analysis of the technology parameter operating range. The results provide evidence that envisioned application performance requirements might be attainable. |
5 |
Technology validated in relevant environment |
Reliability of technology significantly increases. Examples could involve validation of a semi-integrated system/model of technological and supporting elements in a simulated environment. |
6 |
Technology demonstrated in relevant environment |
Prototype system verified. Examples might include a prototype system/model being produced and demonstrated in a simulated environment. |
7 |
System model or prototype demonstration in operational environment |
A major step increase in technological maturity. Examples could include a prototype model/system being verified in an operational environment. |
8 |
System complete and qualified |
System/model produced and qualified. An example might include the knowledge generated from TRL 7 being used to manufacture an actual system/model, which is subsequently qualified in an operational environment. In most cases, this TRL represents the end of development. |
9 |
Actual system proven in operational environment |
System/model proven and ready for full commercial deployment. An example includes the actual system/model being successfully deployed for multiple missions by end users. |
Who uses TRLs?
Originally developed by NASA, TRLs have been taken up by other organisations, including the United States Department of Energy (DOE), the US Department of Defense (DOD), the European Space Agency (ESA), and industries including oil and gas.
Systematic addressing of TRLs is required, allowing a technology to evolve from conception through to research, development and deployment. Universities, along with government funding sources, focus on TRLs 1-4, while the private sector focuses on TRLs 7-9.
The term ‘Valley of Death’ represents the often neglected addressing of TRLs 4 through to 7, where neither academia nor the private sector prioritise investment. Consequently, many technologies, albeit promising, finish their maturity journey prior to deployment.
To bridge the valley of death, collaborative efforts are often required. TWI has a long history of working with its Members and academia, across a range of industry sectors, to fulfil this need. Discussed below are examples of these collaborations.
TWI collaborated with aerospace contractor Airbus Defence and Space to satisfy a European Space Agency request to investigate cost-effective manufacturing methods for titanium alloy propellant tanks. The consortium, making use of TWI’s expertise, raised the TRL of stationary shoulder friction stir welding of titanium alloy propellant tanks to TRL 6.
Collaborating closely with Rolls-Royce, TWI, using laser additive manufacturing, produced nickel alloy seal segments for the Intermediate Pressure stage of a Trent engine. This involved TWI taking the technology from a laboratory stage (TRL 3) through process development to successful engine testing (TRL 7).
TWI has decades of experience working with the automotive industry on a variety of different challenges and technology developments, including electric vehicle battery welding, pushing concepts through to TRL 7 and beyond.
The Non-Metallic Innovation Centre, housed at TWI’s Cambridge facility, was created alongside Saudi Aramco Technologies Company (AramcoTech) and the Abu Dhabi National Oil Company (ADNOC) to investigate and advance the use of non-metallic materials for industrial applications. The centre conducts a research programme covering TRLs 1-9.
Related FAQ: What are Manufacturing Readiness Levels (MRL)?
Have a Question About TRLs?
If you need further help on TRLs please get in touch:
contactus@twi.co.uk